Spray Foam Insulation Solutions for Construction and Renovation Projects
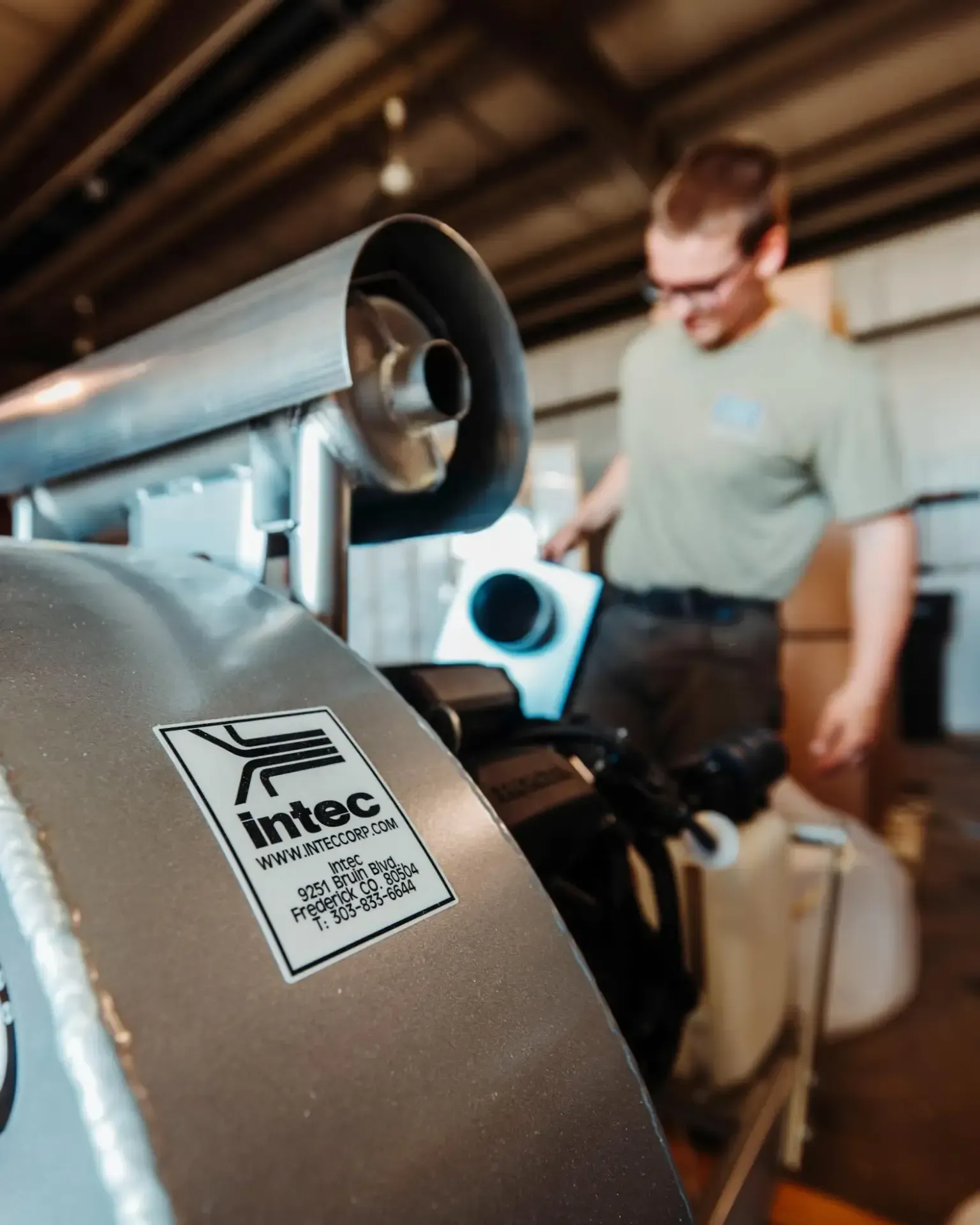
Spray foam insulation has revolutionized construction and renovation projects, offering customers superior insulation for walls, floors, and even pipes. This innovative solution, often made by trusted brands, provides excellent thermal and acoustic properties while sealing gaps and cracks that traditional insulation methods might miss.
For both new builds and home improvements, spray foam insulation delivers critical information on energy efficiency and comfort to property owners. In this article, we’ll explore the various applications and benefits of spray foam insulation for construction and renovation projects.
Key Takeaways
- Spray foam insulation improves energy efficiency and structural integrity in buildings
- Open-cell and closed-cell foam types offer different benefits for various applications
- Professional installation is recommended for large-scale spray foam insulation projects
- Spray foam insulation contributes to achieving green building certifications and sustainability goals
- Building codes and regulations play a crucial role in spray foam insulation implementation
Understanding Spray Foam Insulation Benefits
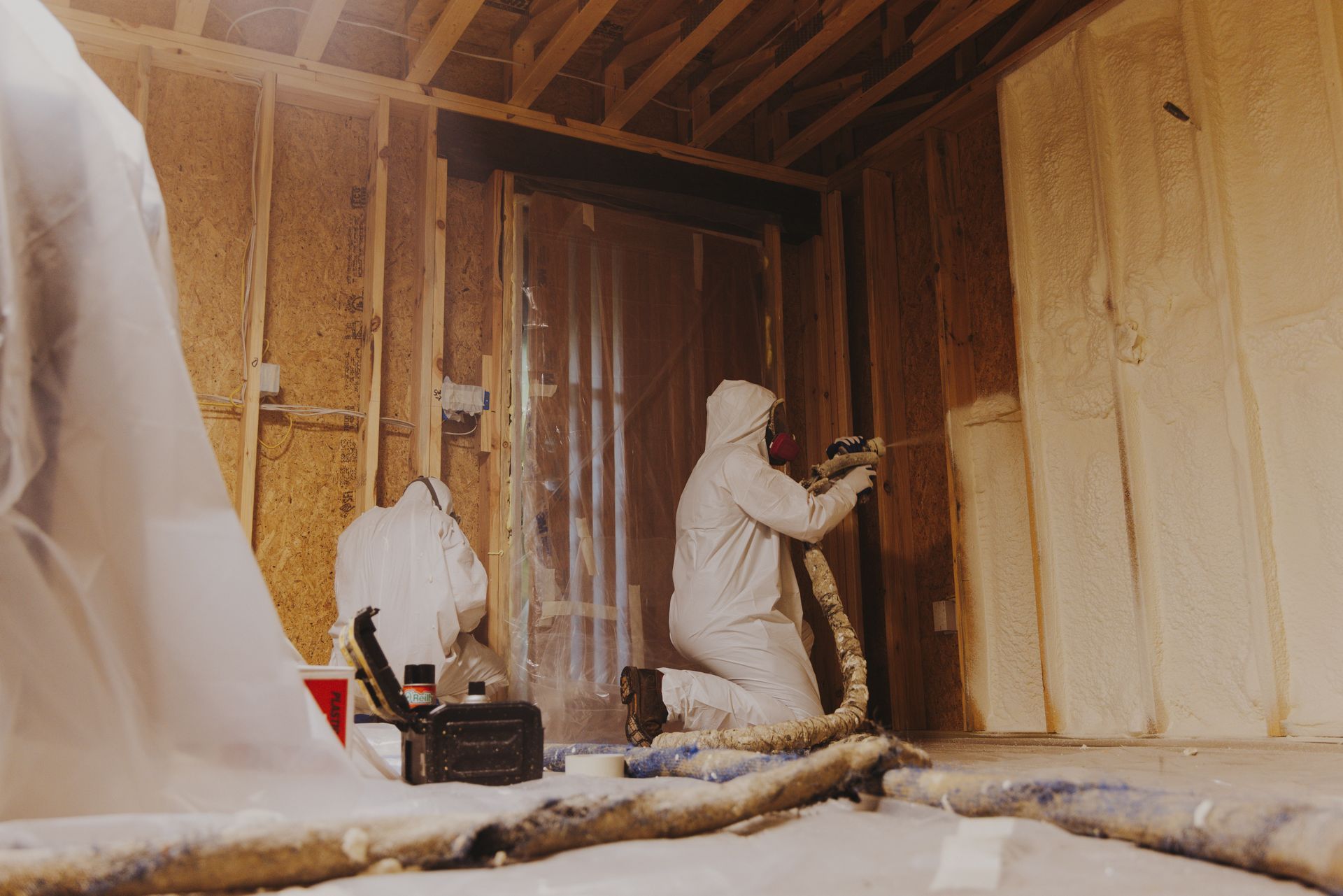
Spray foam insulation has become a popular choice for construction and renovation projects. This versatile sealant offers numerous advantages over traditional fiber-based insulation materials. When applied to walls, roofs, and concrete foundations, the expanding foam creates a tight barrier that significantly improves a building’s performance. Property owners can expect increased energy efficiency, enhanced structural integrity, better air quality, moisture control, and long-term cost savings. These benefits make spray foam insulation an attractive option for both new constructions and existing structures.
Increased Energy Efficiency in Buildings
Spray foam insulation creates a tight building envelope, reducing air leakage and improving energy efficiency. This technology seals gaps and cracks, minimizing pressure differences between indoor and outdoor spaces. As a result, buildings maintain a more stable climate, reducing the workload on heating and cooling systems. The insulation also complements other energy-saving features, such as high-performance windows, to further enhance overall energy efficiency.
Enhanced Structural Integrity
Spray foam insulation strengthens a building’s structure by bonding to surfaces and filling gaps. This creates a barrier against moisture, air leaks, and pests, which can damage walls and foundations over time. During renovation projects, spray foam can seal hard-to-reach areas around plumbing and electrical fixtures, preventing mold growth and improving overall structural integrity.
Improved Air Quality and Moisture Control
Spray foam insulation improves indoor air quality by creating an airtight barrier that prevents the entry of pollutants and allergens. This foam, made from isocyanate and other components, expands to fill gaps and cracks, effectively controlling moisture levels and reducing the risk of mold growth. While spray foam offers these benefits, it’s important to note that proper installation and handling of data related to the process ensures information privacy and safety for property owners.
Long-Term Cost Savings for Property Owners
Property owners who invest in spray foam insulation can expect significant long-term cost savings. This advanced insulation method outperforms traditional fiberglass in reducing energy bills by maintaining consistent indoor temperatures and humidity levels. While the initial cost of spray foam installation may be higher than other options, its durability and efficiency make it a cost-effective choice for both new construction and renovation projects. Homeowners frequently ask about spray foam’s effectiveness in various building materials, including brick, as part of their FAQ process when considering insulation options:
Insulation Type | Initial Cost | Energy Savings | Lifespan |
---|---|---|---|
Spray Foam | Higher | 30-50% | 20+ years |
Fiberglass | Lower | 10-20% | 10-15 years |
Choosing Between Open-Cell and Closed-Cell Spray Foam
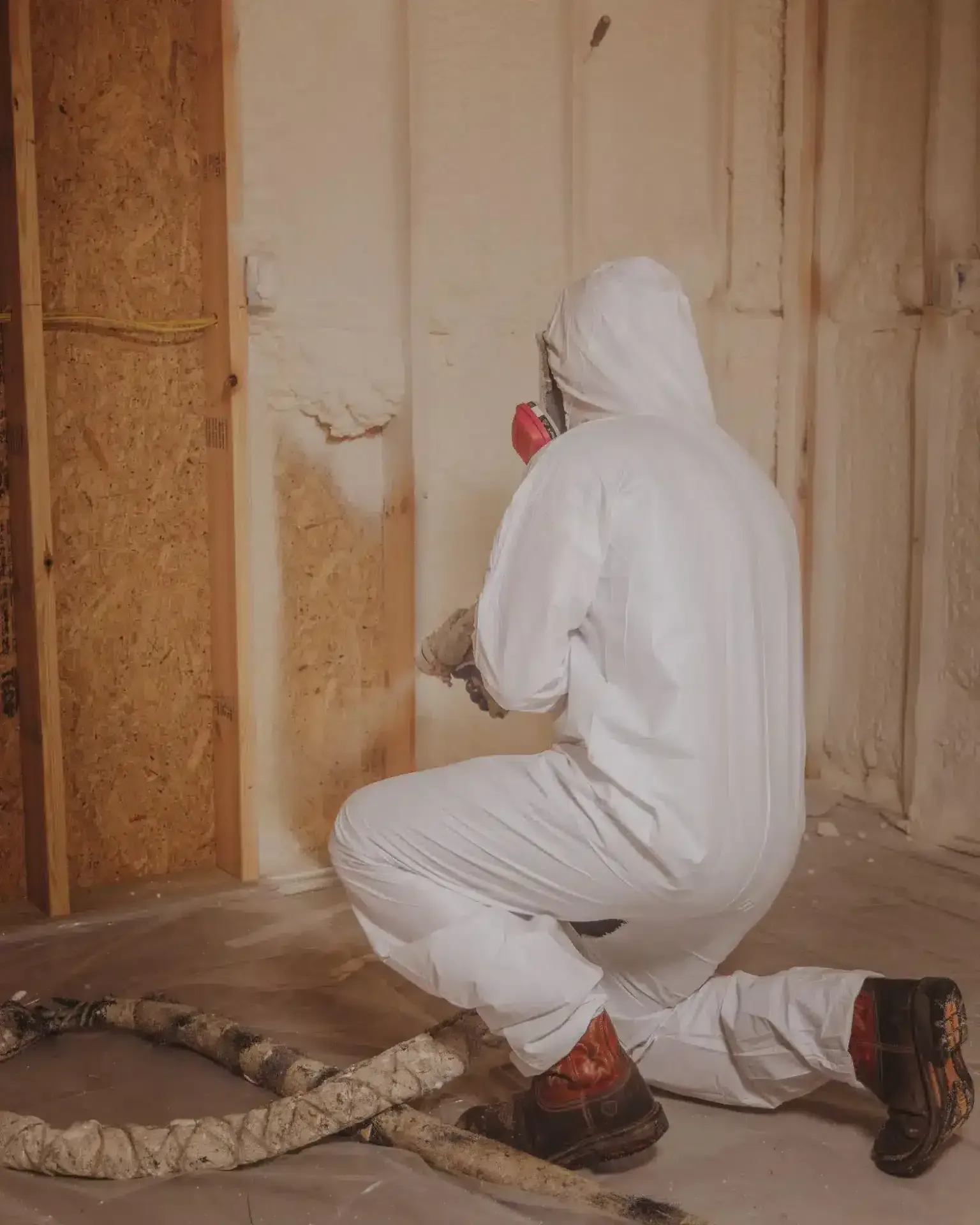
When undertaking home improvement projects involving insulation, property owners must choose between open-cell and closed-cell spray foam. This decision affects thermal resistance, application areas, costs, and overall project needs. While traditional materials like glass wool remain popular, spray foam offers unique advantages for walls and other surfaces. Understanding the differences between these options can save money and improve results. Many construction professionals discuss these choices on podcasts, providing valuable insights for homeowners and contractors alike.
Analyzing Thermal Resistance and Application Areas
Open-cell and closed-cell spray foam insulation offer different thermal resistance properties and application areas. Open-cell foam, with its lower density, is ideal for interior walls, attics, and ceilings, providing excellent sound dampening and allowing for easier access to electrical wiring. Closed-cell foam, being denser and more moisture-resistant, excels in basements, exterior walls, and areas requiring waterproofing. Both types contribute to improved indoor air quality by creating an air-tight seal, but their specific applications depend on the project’s requirements and location within the structure:
Foam Type | Density | R-Value per Inch | Best Applications |
---|---|---|---|
Open-Cell | 0.5-0.8 lbs/ft³ | 3.6 - 3.8 | Interior walls, Attics, Ceilings |
Closed-Cell | 1.7-2.0 lbs/ft³ | 6.0 - 7.0 | Basements, Exterior walls, Roofs |
Cost Comparisons and Budget Considerations
Spray foam insulation costs vary between open-cell and closed-cell types, with closed-cell foam generally being more expensive due to its higher density and superior insulating properties. While open-cell foam is more budget-friendly for large areas like attics or metal roofs, closed-cell foam offers better energy efficiency and moisture resistance, making it ideal for areas prone to water exposure. Homeowners should consider long-term energy savings when comparing spray foam to traditional polystyrene insulation, as the initial investment in spray foam often pays off through reduced utility bills over time. Contractors use specialized tools to apply both types of foam, ensuring proper coverage and maximizing insulation effectiveness.
Determining the Best Fit for Your Project’s Needs
Selecting the right spray foam insulation depends on various factors, including the project’s specific requirements and environmental conditions. Open-cell foam works well for interior applications, such as insulating drywall and wood structures, and offers excellent noise reduction properties. Closed-cell polyurethane foam provides superior moisture resistance and structural support, making it ideal for exterior walls and green building initiatives. Contractors assess factors like climate, building design, and local building codes to determine the most suitable foam type:
- Evaluate project location and climate conditions
- Consider building design and structural requirements
- Review local building codes and energy efficiency standards
- Assess moisture control needs and potential exposure
- Determine sound insulation requirements
- Consider long-term energy savings and sustainability goals
Preparing Your Space for Spray Foam Installation
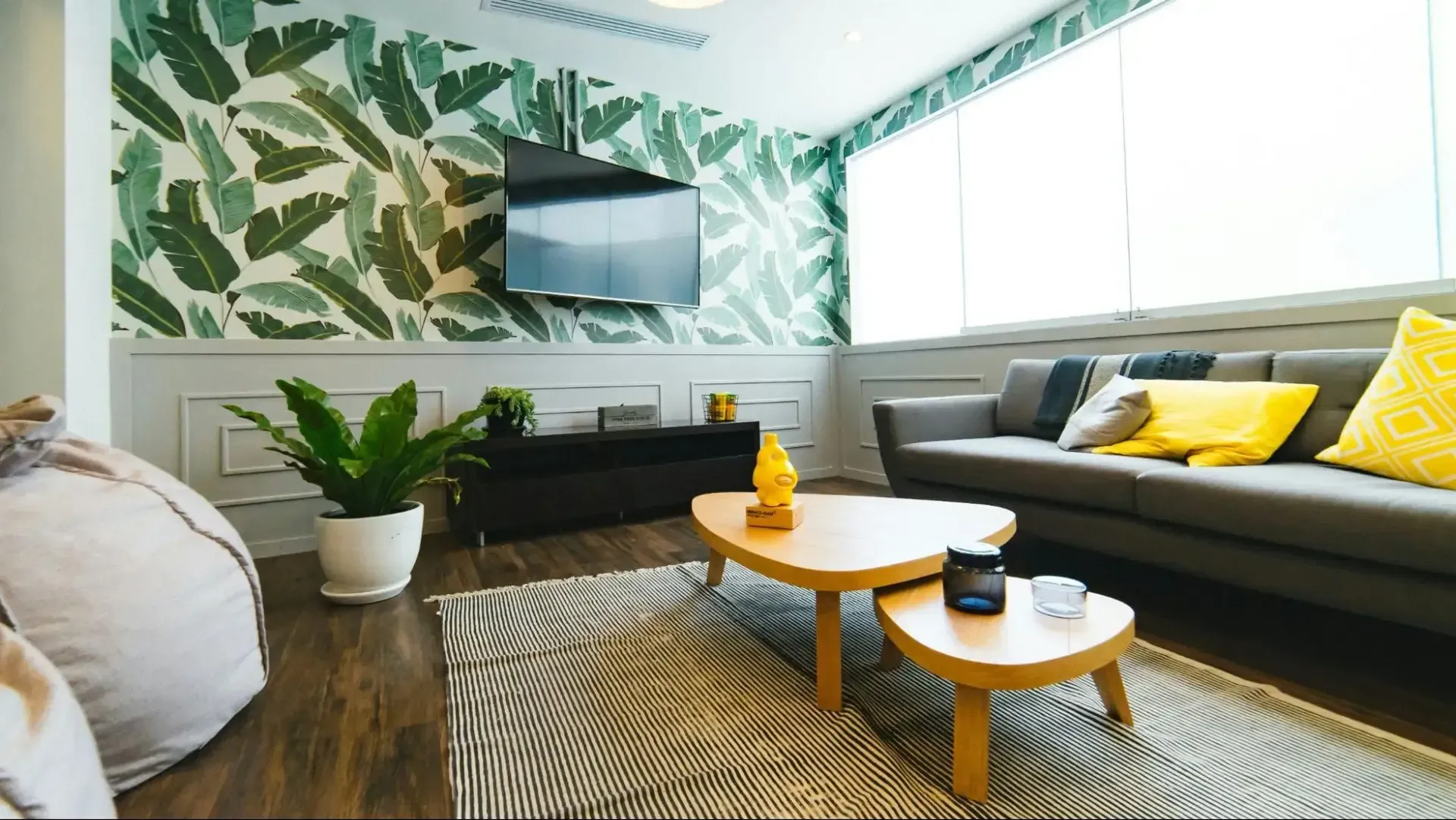
Preparing a space for spray foam insulation is crucial for a successful installation. This process involves clearing the area, protecting sensitive surfaces, ensuring proper ventilation, and identifying critical areas for insulation focus. Homeowners and contractors must consider factors such as attic access, the required inch thickness to meet building codes, and potential sound-dampening benefits. Many professionals offer newsletters with tips on preparing spaces for spray foam application, emphasizing the importance of thorough preparation to maximize energy efficiency and insulation effectiveness.
Clearing the Area and Protecting Sensitive Surfaces
Preparing a space for spray foam insulation requires thorough clearing and protection of sensitive surfaces. This process involves removing all items from the area, including stored belongings in attics or barns. Contractors must cover floors, windows, and other surfaces with protective materials to prevent damage from polyurethane foam overspray. Special attention is given to heat-sensitive elements and areas where the foam’s adhesive properties might cause issues. Before installation, property owners should review the terms of service provided by the insulation company to understand their responsibilities in the preparation process. A well-prepared space ensures optimal application and effectiveness of the spray foam insulation:
- Remove all items from the installation area
- Cover floors, windows, and surfaces with protective materials
- Identify and protect heat-sensitive elements
- Review contractor’s terms of service for preparation guidelines
- Ensure proper ventilation in the work area
- Mark areas requiring special attention or additional insulation
Ensuring Proper Ventilation During Application
Proper ventilation is crucial during spray foam insulation application to ensure safety and optimal results. Contractors must establish adequate airflow in the work area to prevent the buildup of fumes and particulates. This is especially important in enclosed spaces like attics or kitchens, where heat transfer and thermal insulation are key concerns. Proper ventilation also helps maintain the integrity of exterior siding and protects workers and occupants from potential health risks. Installers often use specialized equipment to monitor air quality and may require temporary ventilation systems during the application process:
- Open windows and doors to create cross-ventilation
- Use exhaust fans to remove fumes and particulates
- Install temporary ventilation systems in enclosed spaces
- Monitor air quality throughout the application process
- Allow sufficient time for off-gassing before re-entry
- Follow manufacturer guidelines for ventilation requirements
Identifying Critical Areas for Insulation Focus
Identifying critical areas for insulation focus is essential when installing spray foam. Contractors carefully assess the building’s structure, paying special attention to areas prone to air leakage, such as attics, crawl spaces, and wall cavities. They also examine the building envelope, including roof decks and rim joists, to determine where insulation will have the most significant impact on energy efficiency and comfort.
DIY Spray Foam Insulation Tips for Renovators
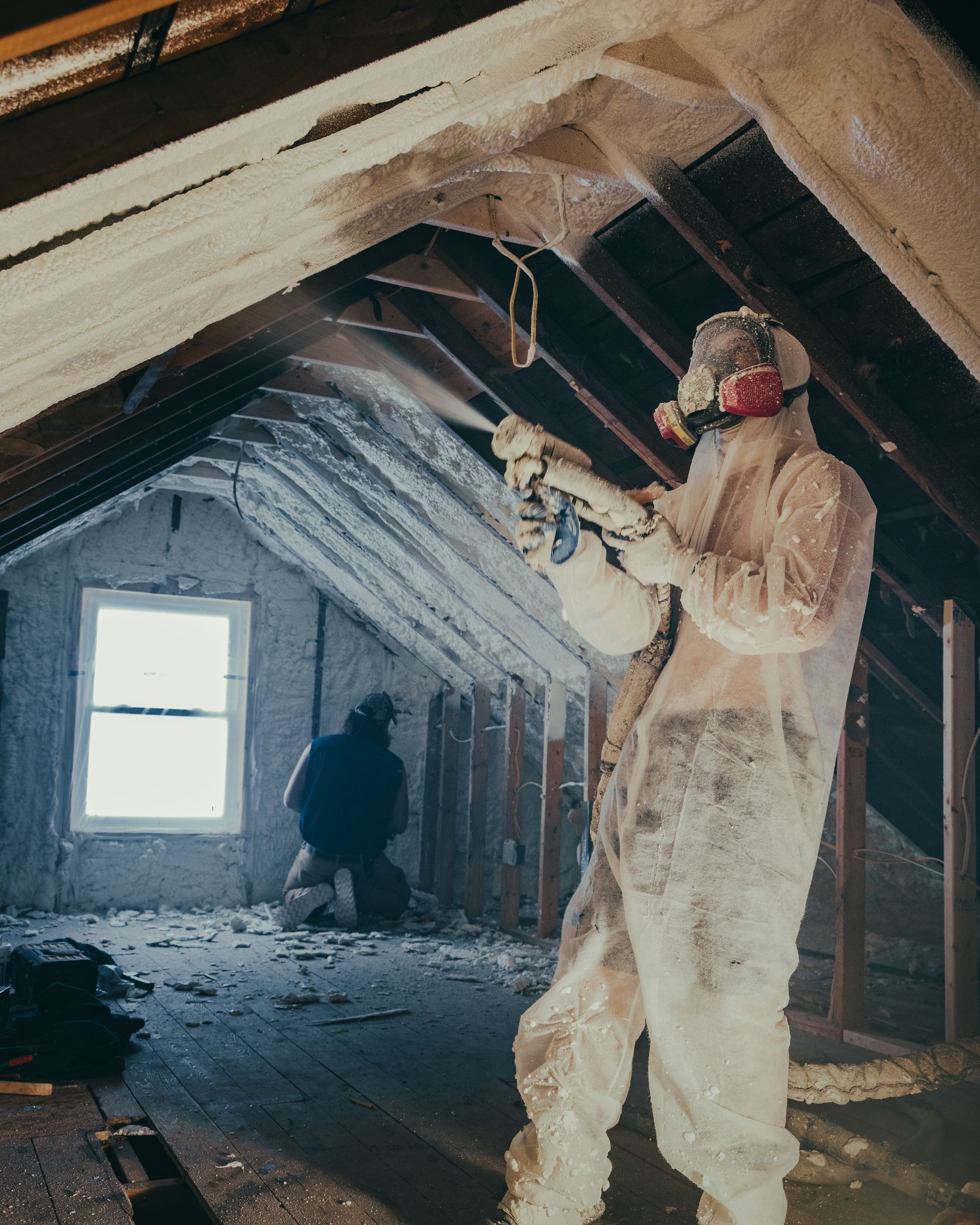
Spray foam insulation offers a cost-effective solution for renovators looking to improve their property’s energy efficiency. While professional installation is recommended for large-scale projects, small-scale applications can be tackled as DIY tasks. Homeowners considering this approach should familiarize themselves with the essential tools, safety gear, and proper application techniques. Understanding the step-by-step process and common challenges helps ensure successful insulation installation. This knowledge empowers renovators to make informed decisions about whether to attempt the project themselves or seek professional assistance.
Essential Tools and Safety Gear for the Job
DIY spray foam insulation projects require specific tools and safety gear. Essential equipment includes a spray foam kit, protective clothing, safety goggles, gloves, and a respirator. Renovators should also have measuring tools, cleaning supplies, and a utility knife on hand. Proper safety precautions are crucial when working with spray foam chemicals:
- Spray foam kit with nozzles and hoses
- Full-body protective suit
- Safety goggles and face shield
- Chemical-resistant gloves
- NIOSH-approved respirator
- Measuring tape and laser level
- Cleaning solvents and rags
- Utility knife for trimming excess foam
- First aid kit
- Fire extinguisher
Step-by-Step Guide For Installers: Applying Spray Foam Correctly
Applying spray foam insulation correctly requires careful preparation and execution. First, ensure the surface is clean, dry, and debris-free. Shake the spray foam canister vigorously for at least 30 seconds before use. Hold the canister upside down and apply the foam in a slow, steady motion, maintaining a consistent distance from the surface. Allow the foam to expand and cure fully before trimming excess material. For larger areas, work in sections to ensure even coverage:
Step | Action | Key Points |
---|---|---|
1 | Surface Preparation | Clean, dry, debris-free |
2 | Canister Preparation | Shake for 30+ seconds |
3 | Application | Steady motion, consistent distance |
4 | Curing | Allow full expansion before trimming |
Troubleshooting Common Application Challenges
DIY spray foam insulation projects often face common challenges that require troubleshooting. Uneven application can result in gaps or excessive buildup, which may be addressed by adjusting the spray technique or nozzle distance. If the foam fails to expand properly, it might indicate an expired product or incorrect mixing ratios, necessitating fresh materials or careful adherence to manufacturer instructions. Sticky or tacky surfaces after curing suggest incomplete chemical reactions, potentially due to temperature fluctuations or inadequate mixing, and may require professional assessment or reapplication.
The Role of Professionals in Spray Foam Insulation
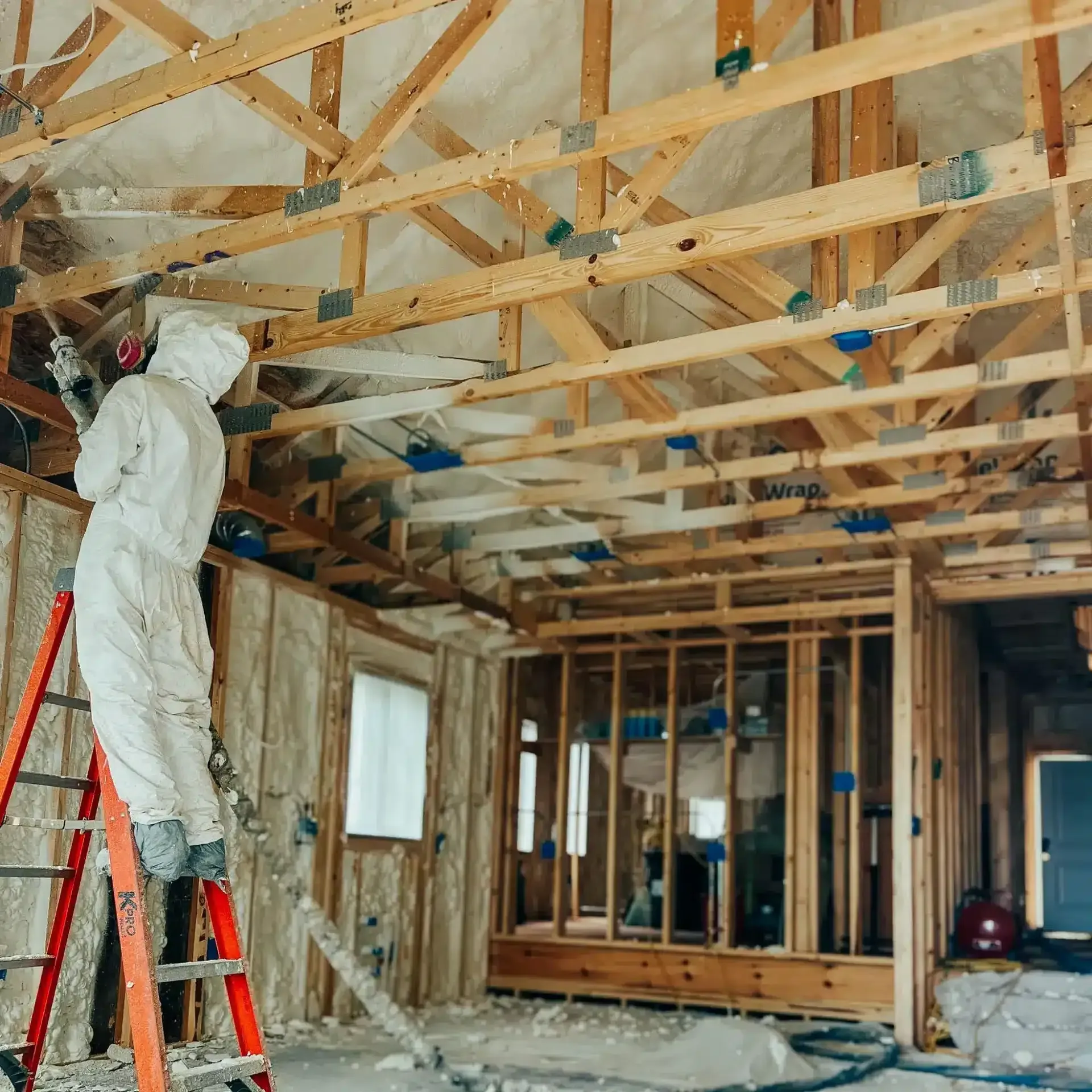
Professional spray foam insulation contractors at Mammoth play a crucial role in ensuring optimal installation and performance. Their expertise becomes invaluable when projects require specialized knowledge or equipment or involve large-scale applications. Understanding when to hire a professional, what to expect during the installation process, and how to select the right contractor are essential aspects of successful spray foam insulation projects. These factors contribute to achieving maximum energy efficiency, proper insulation coverage, and compliance with building codes and safety regulations.
When to Hire a Professional Insulation Contractor
Professional insulation contractors should be hired for large-scale projects, complex installations, or when specialized equipment is required. They bring expertise in handling different types of spray foam, ensuring proper application techniques, and adhering to safety regulations. Homeowners should consider professional help when insulating hard-to-reach areas, dealing with unconventional building structures, or seeking to maximize energy efficiency through precise installation.
What to Expect During the Professional Installation Process
Professional spray foam insulation installation typically begins with a thorough assessment of the property and preparation of the work area. Contractors use specialized equipment to apply the foam evenly, ensuring proper coverage and adherence to safety protocols. Depending on the project scope, the installation process may take several hours to days and often requires temporary relocation of occupants due to fumes and noise.
How to Select the Right Contractor for Your Project
Selecting the right contractor for spray foam insulation involves researching their experience, certifications, and customer reviews. Property owners should request multiple quotes, verify insurance coverage, and ask about the specific products and techniques the contractor uses. A reputable professional will provide clear communication, detailed project timelines, and guarantees for their work.
Spray Foam Insulation for Extreme Climates
Spray foam insulation proves particularly valuable in extreme climates, where maintaining consistent indoor temperatures and energy efficiency poses significant challenges. This advanced insulation method offers superior protection against both intense heat and severe cold, making it an ideal choice for construction and renovation projects in diverse weather conditions. Property owners can achieve optimal thermal performance and long-term cost savings by tailoring insulation choices to withstand severe weather. Examining case studies of successful implementations in hot and cold environments provides valuable insights into the effectiveness of spray foam insulation across different climate zones. Additionally, understanding proper maintenance techniques ensures the long-term efficacy of spray foam insulation in harsh climates, maximizing its benefits for years to come.
Tailoring Insulation Choices to Withstand Severe Weather
Spray foam insulation choices must be tailored to withstand severe weather conditions in extreme climates. Closed-cell foam offers superior moisture resistance and structural strength, making it ideal for areas prone to hurricanes or heavy snowfall. In hot, arid regions, open-cell foam provides excellent thermal insulation while allowing walls to breathe, preventing moisture buildup.
Maintenance Tips for Long-Term Efficacy in Harsh Climates
Maintaining spray foam insulation in harsh climates requires regular inspections and prompt repairs to ensure long-term efficacy. Property owners should check for signs of wear, such as cracks or gaps, especially after extreme weather events. Addressing any issues quickly prevents moisture intrusion and maintains the insulation’s thermal performance, protecting the building from the effects of severe hot or cold temperatures.
Sustainability and Eco-Friendliness of Spray Foam
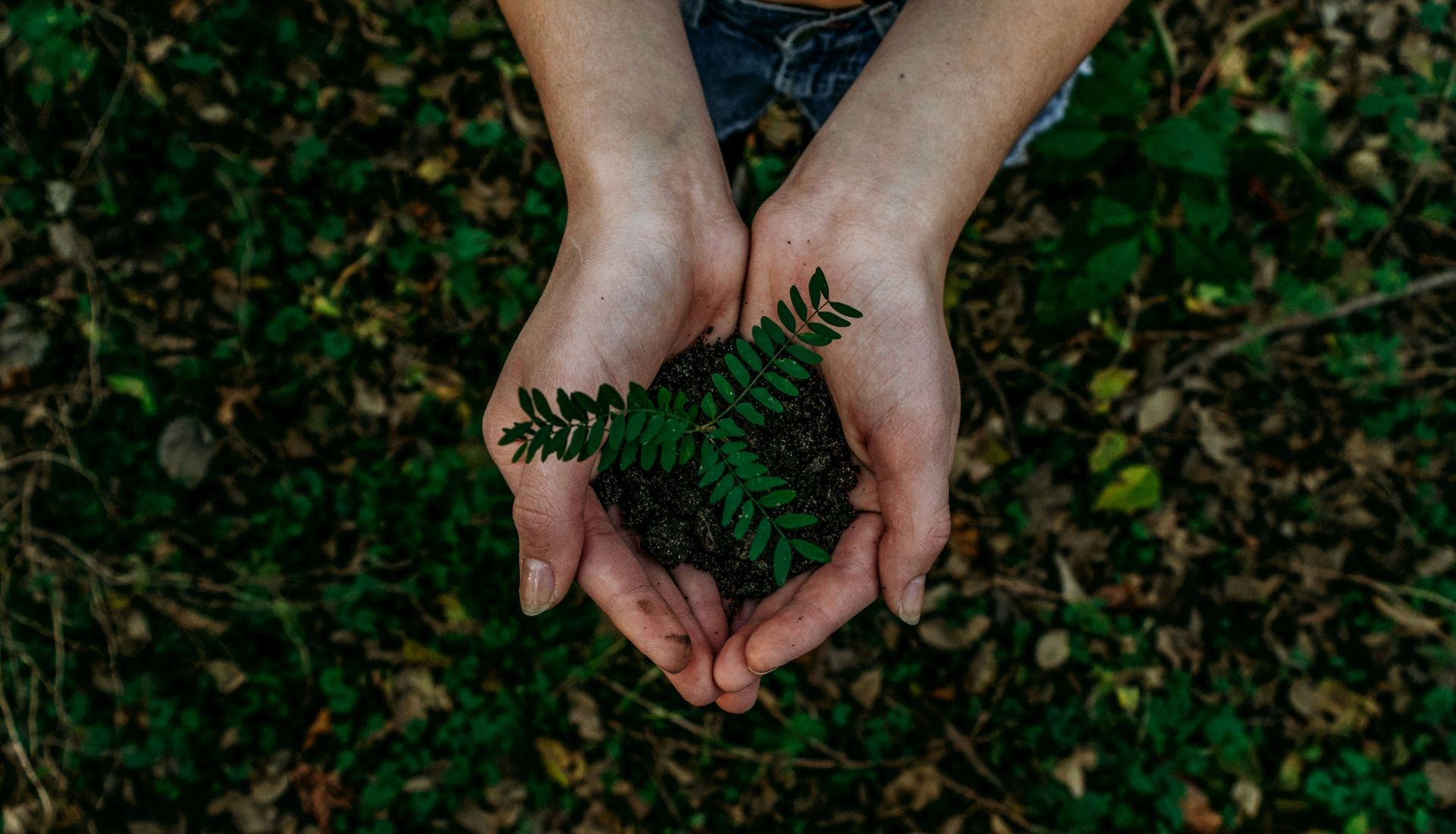
Spray foam insulation’s sustainability and eco-friendliness have become increasingly important in the construction industry. As builders and homeowners seek greener alternatives, understanding the environmental impact of spray foam products is crucial. This includes examining their production processes, long-term energy-saving benefits, and potential effects on indoor air quality. The market now offers low-VOC (Volatile Organic Compound) spray foam options, which address concerns about chemical emissions while maintaining insulation efficiency. Furthermore, proper insulation plays a significant role in achieving green building certifications, contributing to overall energy efficiency and sustainable design practices in both new constructions and renovation projects.
Understanding the Environmental Impact of Spray Foam Products
Spray foam insulation products have both positive and negative environmental impacts. On the positive side, they significantly reduce energy consumption in buildings, leading to lower greenhouse gas emissions over time. However, some spray foam products contain chemicals that can harm the ozone layer and contribute to global warming if not properly handled and disposed of.
Selecting Greener, Low-Voc Spray Foam Options
Low-VOC spray foam options offer a greener alternative for environmentally conscious property owners. These products reduce the emission of harmful volatile organic compounds during and after installation, improving indoor air quality and minimizing environmental impact. Selecting low-VOC spray foam insulation aligns with sustainable building practices and can contribute to achieving green building certifications:
- Lower environmental impact during production and installation
- Improved indoor air quality for occupants
- Reduced emission of harmful chemicals
- Compatibility with green building standards
- Maintained insulation efficiency and performance
The Role of Insulation in Achieving Greener Building Certifications
Spray foam insulation plays a crucial role in achieving greener building certifications. It contributes significantly to energy efficiency, a key factor in rating systems like LEED (Leadership in Energy and Environmental Design) and ENERGY STAR. By providing superior thermal insulation and air sealing, spray foam helps buildings meet stringent energy performance requirements, ultimately leading to higher certification levels and more sustainable structures.
Innovations in Spray Foam Insulation Technology

Spray foam insulation technology continues to evolve, offering improved performance and efficiency for construction and renovation projects. Recent innovations have led to the development of more environmentally friendly formulations, enhanced application methods, and advanced thermal properties. These advancements make spray foam insulation increasingly effective in creating energy-efficient building envelopes. As the industry looks to the future, emerging trends point towards smart insulation systems, bio-based materials, and integration with other building technologies to optimize energy performance and sustainability in residential and commercial structures.
Latest Advancements in Insulation Materials and Techniques
Recent advancements in spray foam insulation materials and techniques have led to improved performance and sustainability. New formulations incorporate renewable resources and recycled content, reducing the environmental impact of insulation production. Application techniques have evolved to include precision spraying equipment and robotic systems, ensuring more consistent coverage and reducing waste during installation.
How New Technologies Are Making Spray Foam More Effective
New technologies are enhancing the effectiveness of spray foam insulation through improved chemical formulations and application methods. Advanced blowing agents and polymer compositions result in higher R-values per inch, providing better thermal performance in thinner applications. Computer-controlled spraying systems ensure precise mixing ratios and consistent foam density, leading to more uniform coverage and improved overall insulation quality:
- Enhanced chemical formulations for higher R-values
- Computer-controlled spraying systems for precise application
- Improved blowing agents for better foam expansion and adhesion
- Advanced polymer compositions for increased durability
- Real-time monitoring systems for quality control during installation
Future Trends in Building Insulation Solutions
Future trends in building insulation solutions point towards the integration of smart technologies and sustainable materials. Researchers are developing spray foam insulations with phase-change materials that can store and release heat, actively regulating indoor temperatures. Bio-based foams derived from plant sources show promise as eco-friendly alternatives to traditional petroleum-based products, aligning with growing demands for sustainable construction practices.
Conclusion
Spray foam insulation offers significant benefits for construction and renovation projects, including increased energy efficiency, enhanced structural integrity, improved air quality, and long-term cost savings. Property owners must carefully consider factors such as insulation type, application methods, and local building codes to maximize the effectiveness of their spray foam installations. While DIY applications are possible for small-scale projects, professional contractors bring the expertise and specialized equipment necessary for large-scale or complex installations. As spray foam technology continues to advance, it plays an increasingly important role in creating sustainable, energy-efficient buildings that meet the demands of extreme climates and evolving environmental standards.
Share On: